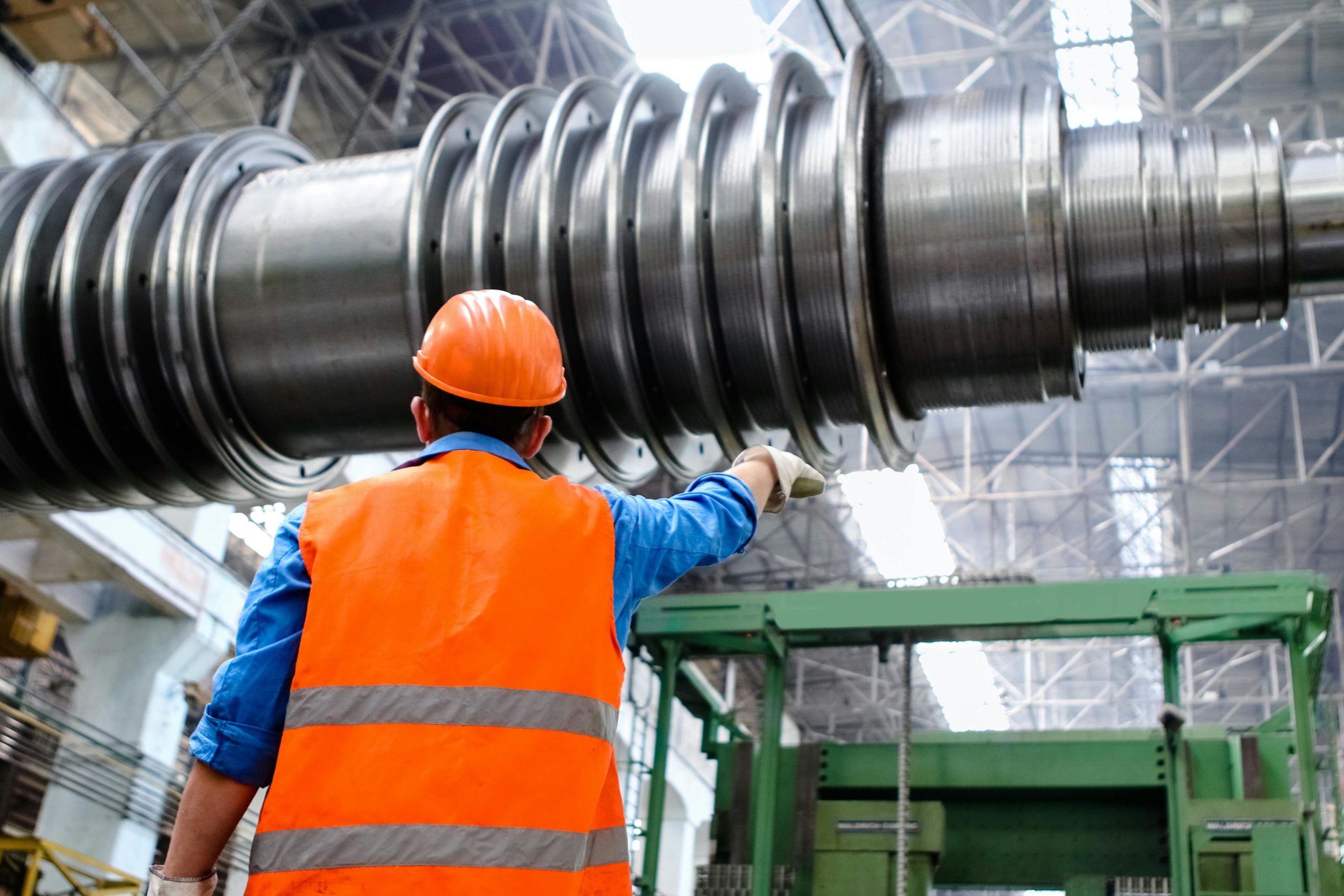
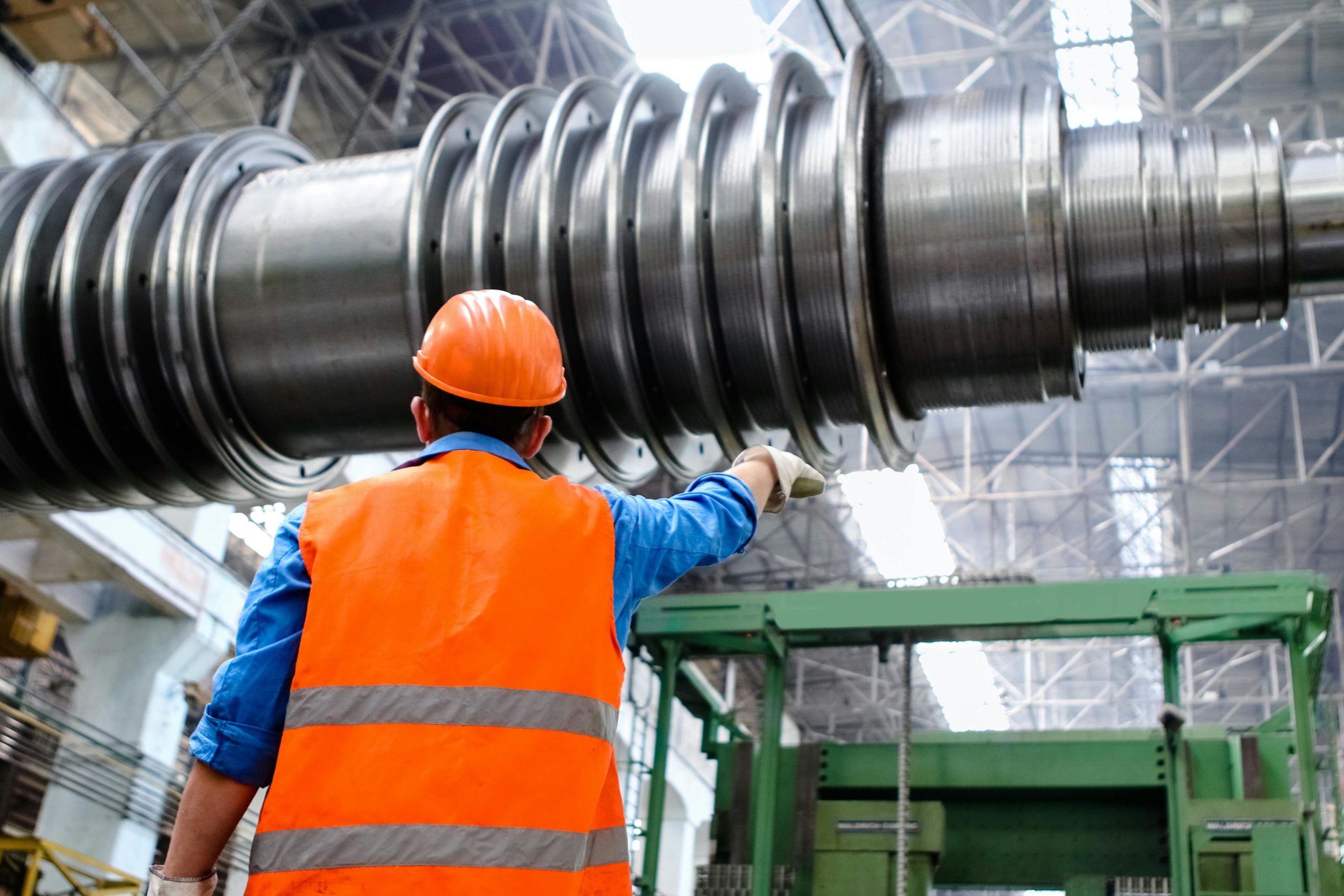
Maintenance: waste & time on work orders
18 July 2024‘I’m fascinated by Lean’s focus on waste in day-to-day operations. I believe that using the same ‘Lean mindset’ for the maintenance process is beneficial not only for the company but also for the environment. However, this Lean approach to maintenance needs to be seen in a different light to the Lean approach to production.
Lean cannot be confined to production
For Lean production to be successful, maintenance must also be Lean. Keeping the same basic definition, even if the environment is different, improves communication with production and other functions. However, Lean maintenance differs from production, for example because maintenance work has to be planned, whereas production work can be ‘pulled’ by customer orders. Interestingly, there is one similarity: both require careful planning based on the actual capabilities of the machines, whether it’s production or preventive maintenance. Finding Muda or Muri and eliminating them should be part of everyone’s daily activities.
Maintenance could even be divided into 2 phases: the management of work orders and the execution of the maintenance itself’.
Would you say that Lean thinking is more about production than maintenance?
There are a lot of articles about waste in maintenance and that’s great!
A maintenance department would be well advised to create a small database listing examples of waste in maintenance identified by its mechanics or electricians, to communicate on it and to keep it alive.
The basics will always be the same, but depending on the company and the culture, there may be slight differences. Above all, discussing these issues and finding solutions with the team will help the maintenance department to develop further.
From a reactive to a proactive culture
When helping a maintenance department move to a proactive culture, one of the fundamental elements is certainly the planning of maintenance work. Whatever advanced tools you use, your success will also depend on creating the work plan for each task. When it comes to planning, a variety of information is needed, but to create a good weekly schedule, time estimates are crucial.
As we all know, realistic task estimates are not only essential for planning, but also for coordinating, controlling and motivating technicians.
So don’t expect a young/new planner to be able to estimate the time needed for tasks if they don’t have an explanation of the existing methods and processes to be followed. Consequently, breaking down the work into major stages is the first action that needs to be taken.
The maintenance department will start simply and refine the approach as it matures.
How can maintenance working time be estimated as accurately as possible?
Initially, the planner(s) will use simple estimates. The estimates reflect a personal judgement and will depend on the experience of each planner.
There are two main problems with estimates:
- There is a risk of inconsistency between planners.
- Estimates reflect the time they think the job will take (not the time the job should take).
However, the advantage of this method is that it doesn’t require too much effort, so it’s a good start.
Over time, enough data will become available for the planner to use historically based data. Peaks and valleys should be eliminated and we’ll be able to calculate averages. This will depend on complete and accurate data capture, a good feedback loop and therefore good communication between the planner and the technicians.
The problem here is that even if this stage of the process is well set up, if we’re looking for excellence in maintenance these averages won’t be enough. We need to find a way of improving these estimates still further.
The next step is to use adjusted historical data. To do this, it is necessary to measure the efficiency of the team by measuring the actual time spent on each task, in particular through observations. Feeding the historical data with the actual efficiency measured will enable a new estimate to be made of the time the job should take in future. Don’t forget to take action to eliminate the inefficiencies discovered during the observations. This is the start of creating standards. Don’t forget that carrying out observations is a cost factor for the maintenance department. Observations should therefore be used as a basis to show the department what needs to be improved and how everyone can contribute. Introducing this change will help to make the department more efficient without leading to haste (muri) and dangerous behaviour within the teams.
From an observational to an analytical estimation method
The analytical estimating method is another structured way of determining time estimates and an approach to developing standards for maintenance work. In this method, you develop a sequence of work that applies to the majority of your jobs or the way they should normally be carried out (ideally, for shorter jobs, you will ignore certain stages). For each of these steps, create a table with three levels of difficulty and set values for them. For example, one table could contain the times associated with instruction, preparation and feedback for simple, medium and complex jobs. Another table would contain the travel times to different areas for simple, medium and complex tasks. Another table for the history of maintenance work by equipment.
There may be other methods and each company can develop its own method. To be successful, the most important point is to inform all the participants of the reason for introducing first the estimates and then the standards. We want the equipment to be operational, so we need to make every effort to give production a better indication of how long the equipment will be unavailable. To give everyone the opportunity to be an observer and make a contribution where inefficiencies occur, to participate in improving the maintenance function.
Speaking of participation, you’ll probably hear that every task is different and that it’s impossible to correctly estimate the duration of each maintenance task.
This is true, but is it really necessary to be 100% correct?