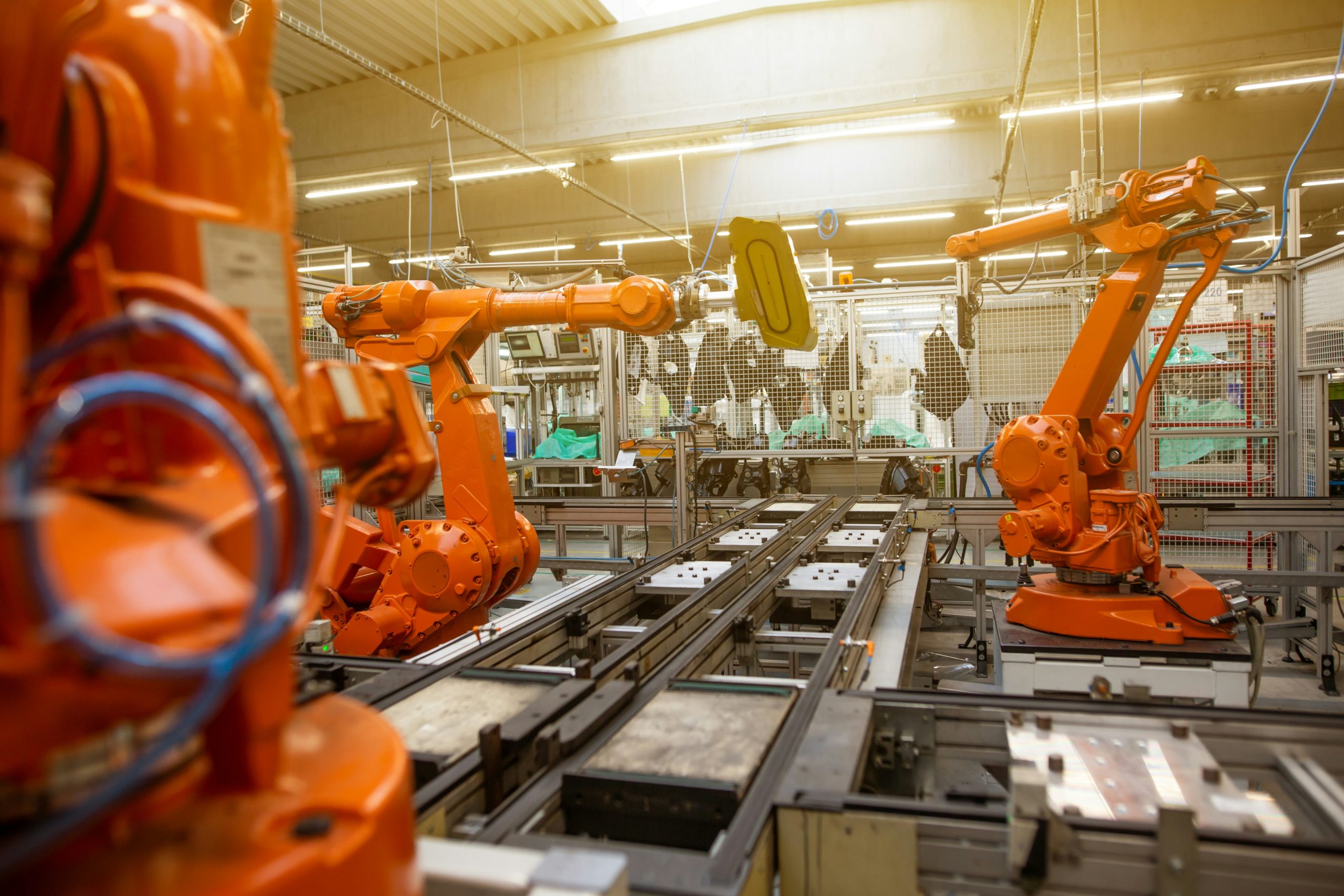
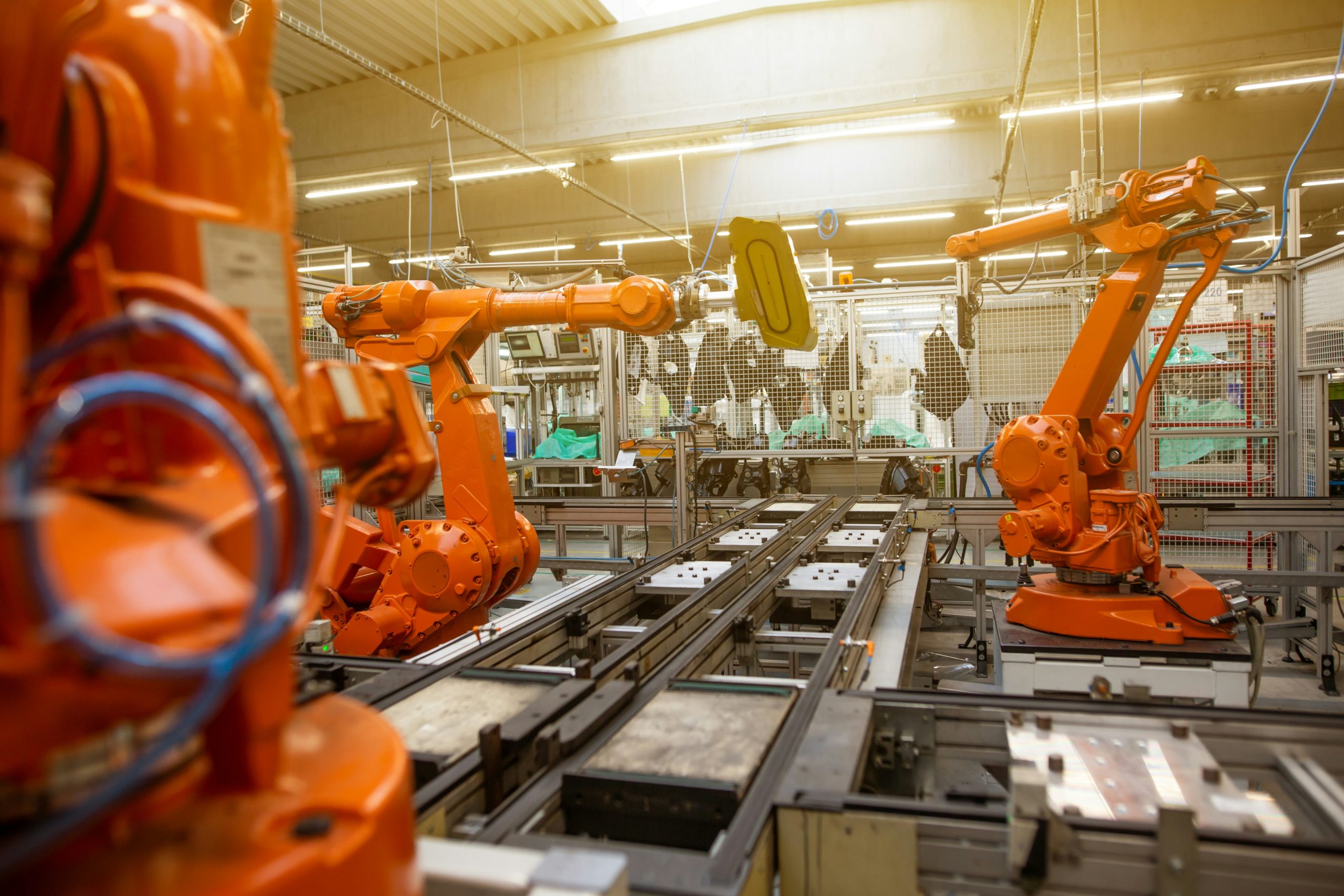
Optimising production facilities and cutting costs
Spirit Advisors is specialised in operational excellence for industry. We help you to optimise your production facilities and reduce your operating costs.
Protection against crisis
Operational optimisation is crucial in a context where instability has become the norm, and where the reconfiguration of the industrial sector is becoming an inescapable trend, operational optimisation is becoming crucial. You are faced with stable volumes, but competitive pressure, inflationary pressures and the need to protect your wage bill are forcing you to reduce your production costs and secure your purchases. For some of your industrial sites, this is even a question of survival.
The hunt is on to reduce waste and optimise assets: overproduction, overstocking, under-quality, rejects, waste, late deliveries, low levels of automation, excessive energy consumption, etc. All the causes of cost overruns need to be meticulously analysed and dealt with.
The best way to reduce your costs is to establish a collective culture of performance and continuous improvement. A trained and empowered team, supported by responsive management, is the keystone of this approach.
Revealing hidden
potential
Looking for waste
Our observations in the field indicate an average of around 40% of high added value activities in industry. A significant leap in performance is within your grasp! Our analyses enable us to identify hidden potential with your teams, with whom we co-build appropriate solutions that will be tested and adjusted as they develop to a new norm.
Making your managers proactive
75% of a field manager’s time is spent reactively. It’s a vicious circle, and they end up breaking down, or coming to terms with it and becoming the “superheroes” who save the plant every day… By sharing their daily lives, and helping them to solve their problems, we support field managers so that they can have a real impact, proactively.
Reviewing your management system
A production facility is punctuated by daily routines or rituals, and behaviour is guided by feedback teams receive on their performance, and by the questioning and support of their hierarchy. Together with your teams in the field, we question the various existing elements of the field management system in order to move on to the next level.
Launching a collaborative Lean Management program
Lean is a pair of glasses that allows you to see production sites differently, making the waste that is invisible in the indicators and the multiple reports visible. Your employees will benefit from the Lean experience either by joining the project team with our consultants, or by following our training-action courses.
Major benefits
of optimising production facilities
Reduced costs
Reduce production and storage costs
Increased quality
Eliminate waste and delays and improve overall quality
Happy relationships
Set up a collective culture of performance and improve supplier relations
Stabilising delays
and ensuring the long-term future of the site
Our client is a major supplier to the aerospace industry. It plays a critical role in aircraft assembly.
One of its industrial sites is experiencing chronic delivery delays, putting its customer’s assembly lines at risk. It also had to drastically reduce its production costs to ensure the site’s long-term viability.
A Spirit Advisors team spent 6 months on site, optimising manual assembly lines and removing bottlenecks in the manufacture of certain components.
Spirit Advisors’ distinctive point : Involving external logistics players and helping production supervisors to adopt new behaviours, in conjunction with HR and management, has helped to improve the site’s overall performance.